How Coconut Husk Chips Are Made: A Transparent Look at the Production Process
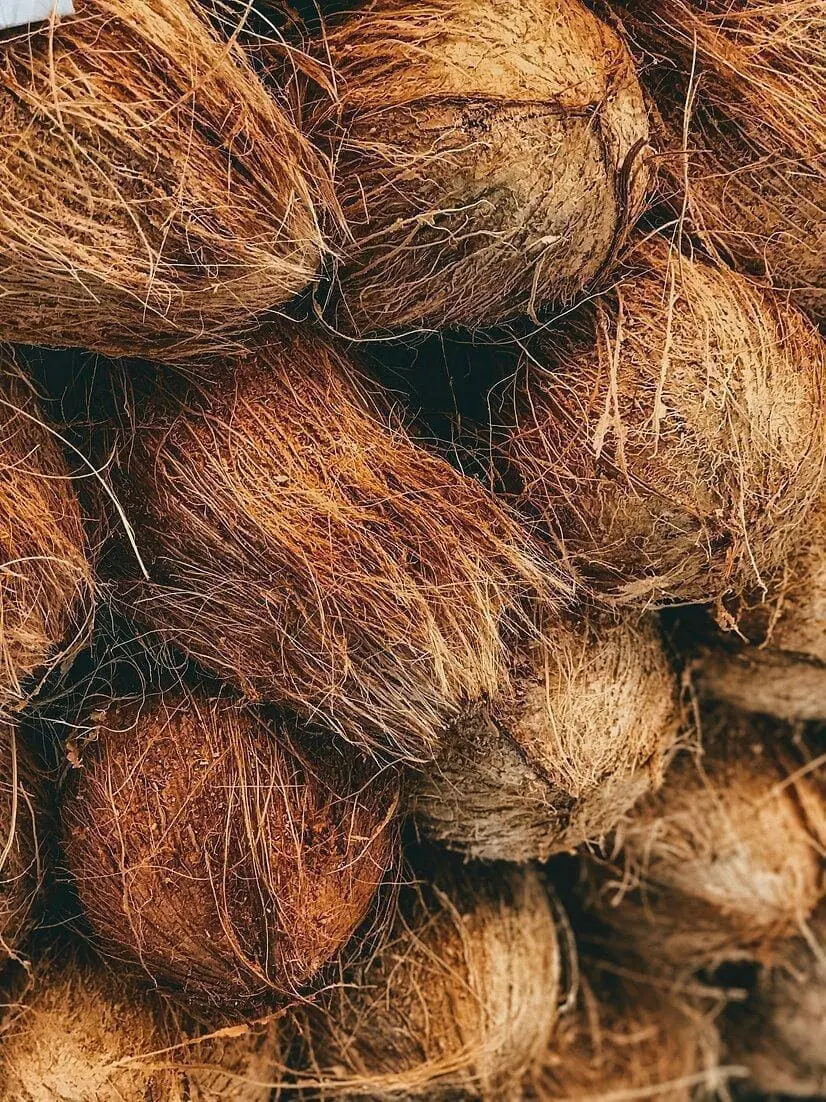
Coconut husk chips are becoming more popular because they’re eco-friendly and useful in many ways. People use them for gardening, farming, and even industrial purposes. But how exactly are these chips made?
At Vagaa.lk , we believe transparency builds trust. That’s why we’re showing you the step-by-step process of turning raw coconut husks into high-quality products. Whether you’re a curious buyer or an industry professional, this guide will help you understand why Sri Lanka is a global leader in producing coconut husk chips.
Why Coconut Husk Chips Are in Demand
Eco-Friendly and Versatile
Coconut husk chips are biodegradable, renewable, and incredibly versatile. Here’s why people love them:
- Gardening: They improve soil aeration and water retention.
- Farming: Farmers use them to prevent soil erosion and retain moisture.
- Industry: Manufacturers rely on them for sustainable packaging and biofuel production.
Applications Across Industries
These chips serve multiple purposes:
- Gardeners appreciate their ability to enhance plant growth.
- Farmers find them helpful for protecting soil health.
- Manufacturers value them as a green alternative to synthetic materials.
Transparency Builds Trust
Customers want to know how products are made. When companies share this information, it reassures buyers about quality and sustainability. Now, let’s dive into the details of how coconut husk chips are made, step by step.
Step 1: Sourcing Raw Materials
Harvesting Coconuts
The process starts with harvesting coconuts from plantations across Sri Lanka. Sri Lanka’s tropical climate allows it to produce millions of coconuts every year. These coconuts provide the raw material needed to create husk chips.
Pro Tip: Fresh, high-quality husks are essential for making durable and effective chips.
Separating Husks from Coconuts
After harvesting, workers remove the fibrous outer layer (husk) from the inner shell. This can be done manually or using machines. Once separated, the husks are collected and prepared for the next stage.
Transition: With the husks ready, the next step involves cleaning and preparing them for processing.
Step 2: Cleaning and Preparing the Husks
Removing Impurities
Before processing, workers clean the husks thoroughly to remove dirt, debris, and any leftover shell fragments. This ensures the final product is safe and hygienic for use.
Tip: Cleanliness is especially important for applications like hydroponics and gardening.
Soaking and Softening
To make the husks easier to work with, they are soaked in water. Soaking softens the fibers and helps remove excess salts and impurities. Additionally, this step prepares the husks for shredding.
Transition: Once softened, the husks move on to the next stage: shredding and chipping.
Step 3: Processing the Husks into Chips
Shredding and Chipping
Workers feed the softened husks into shredding machines. These machines cut the husks into uniform chips. Depending on customer needs, the chips can vary in size:
- Fine chips work well for hydroponics and seedling nurseries.
- Larger chips are ideal for mulching and erosion control.
Pro Tip: Customizing chip sizes allows producers to meet diverse customer requirements.
Drying the Chips
After shredding, the chips are dried to reduce moisture content. Drying happens either naturally under the sun or in industrial dryers. Proper drying ensures the chips remain durable and free from mold or rot during storage.
Transition: Once dried, the chips undergo rigorous quality checks before packaging.
Step 4: Quality Control and Packaging
Ensuring Consistency and Quality
Quality control is a critical part of the process. Workers inspect each batch of chips for:
- Size consistency
- Moisture levels
- Cleanliness
This ensures the product meets industry standards and customer expectations.
Tip: High-quality chips perform better in gardening, farming, and industrial applications.
Packaging for Distribution
Finally, workers pack the chips in eco-friendly bags or bulk containers for shipping. Labels include details about origin, size, and usage instructions, making it easy for buyers to understand the product.
Transition: Now that we’ve covered the production process, let’s explore why Sri Lanka stands out as a leader in this industry.
Why Sri Lanka is a Leader in Coconut Husk Chip Production
Abundant Coconut Resources
Sri Lanka’s tropical climate and extensive coconut plantations provide a steady supply of raw materials. This abundance makes Sri Lanka an ideal location for producing coconut husk chips.
Skilled Workforce and Sustainable Practices
Local workers bring expertise to the process, ensuring high-quality, eco-friendly products. Additionally, producers prioritize environmentally responsible practices, from sourcing to packaging.
Global Export Hub
Sri Lanka exports coconut husk chips worldwide, meeting international demand for sustainable materials. Buyers trust Sri Lankan products for their quality and reliability.
Transition: Now that you know how coconut husk chips are made, let’s discuss how you can benefit from this amazing product.
Conclusion: Building Trust Through Transparency
Understanding the production process of coconut husk chips builds trust and confidence in the product. Every step, from sourcing raw materials to packaging the final product, focuses on quality, sustainability, and transparency.
Ready to experience the benefits of high-quality coconut husk chips? Visit our selling page to learn more and place your order today! Whether you’re a gardener, farmer, or industry professional, our products are crafted to meet your needs while supporting eco-friendly practices.
Together, let’s create a greener future—one coconut husk chip at a time! 🌿
Frequently Asked Questions (FAQs)
What Are Coconut Husk Chips Used For?
They are used in gardening, agriculture, and industrial applications like mulching, soil conditioning, and packaging.
How Are Coconut Husk Chips Different from Cocopeat?
While both come from coconut husks, cocopeat is finer and used as a growing medium, whereas husk chips are larger and used for mulching or erosion control.
Are Coconut Husk Chips Eco-Friendly?
Yes, they are biodegradable, renewable, and support sustainable practices.
How Long Does It Take to Produce Coconut Husk Chips?
The entire process, from sourcing to packaging, typically takes 1-2 weeks, depending on the scale and drying method.
Order now: vagaa.lk